設備ごとの電力見える化で、エネルギーのムダを把握。データに基づいた改善提案が可能に【導入事例|株式会社有沢製作所】
- IoT電力センサ
- SIRCクラウド
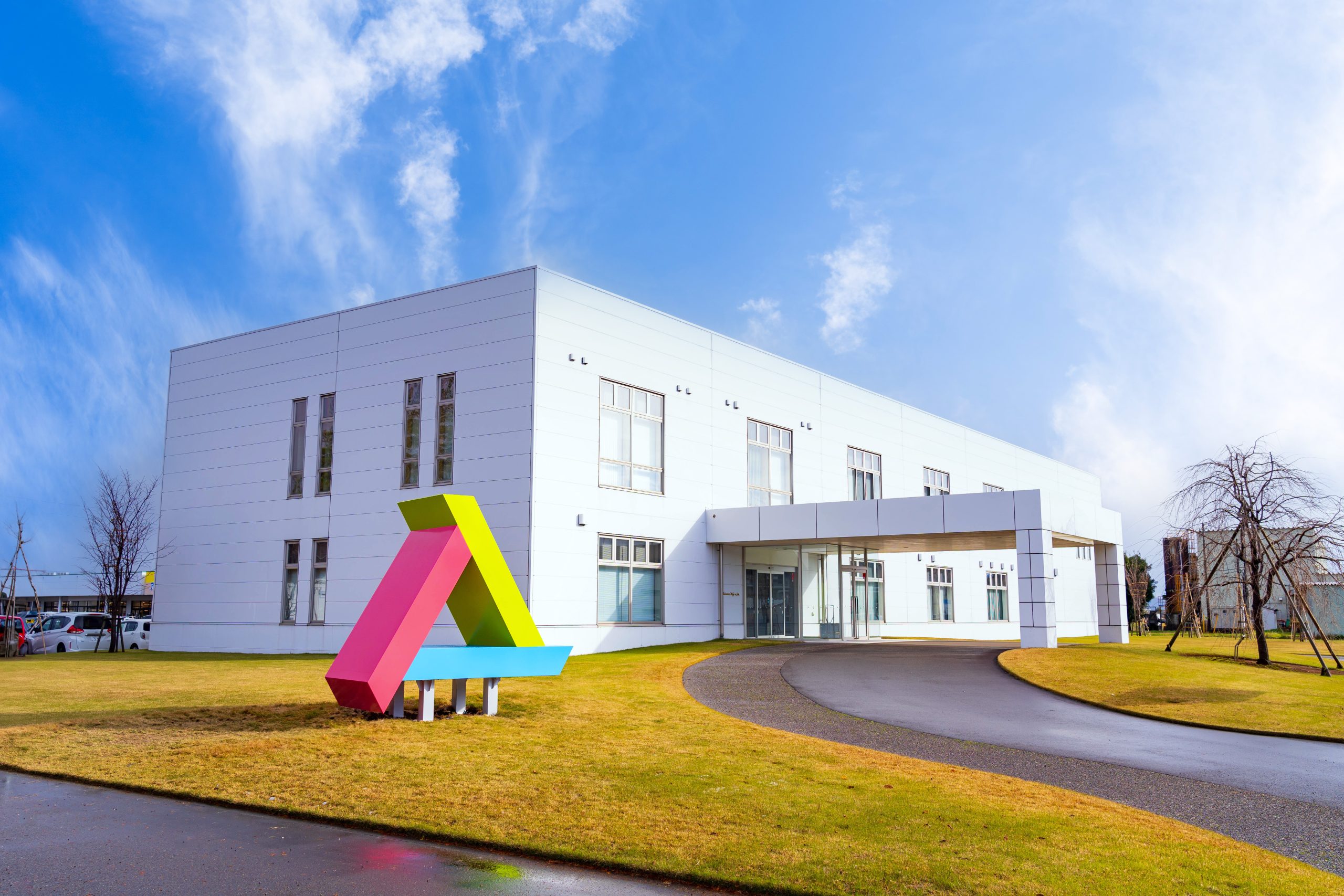
1909年に新潟県上越市でバテンレース※の製造から始まった株式会社有沢製作所。現在はスマートフォンの電子材料や航空機の内装材、医療用3Dディスプレイ材料など、幅広い分野での製造・販売と研究開発を行っています。
2025年には、従来の建物に必要なエネルギーを50%以上削減する「ZEB Ready」を目指したイノベーションセンターの開設を予定するなど、気候変動に関する課題にも積極的に取り組まれています。
今回は、同社の生産本部 生産技術部 電気グループの芥川様に IoT電力センサユニット と SIRCクラウド についてお話を伺いました。
※バテンレース:インテリアとして使用される、ドイツ発祥のレース工芸品。(参考:新潟県HP)
導入サービス
設備ごとの電力見える化で、エネルギーのムダを把握。
データに基づいた改善提案が可能に
―貴社の事業内容を教えてください。
「織る」「塗る」「形づくる」の技術を基に、電子材料や電気絶縁材料、ディスプレイ材料など、ITを中心とした私たちの暮らしを支えるさまざまな製品の製造・販売と研究開発に取り組んでいます。
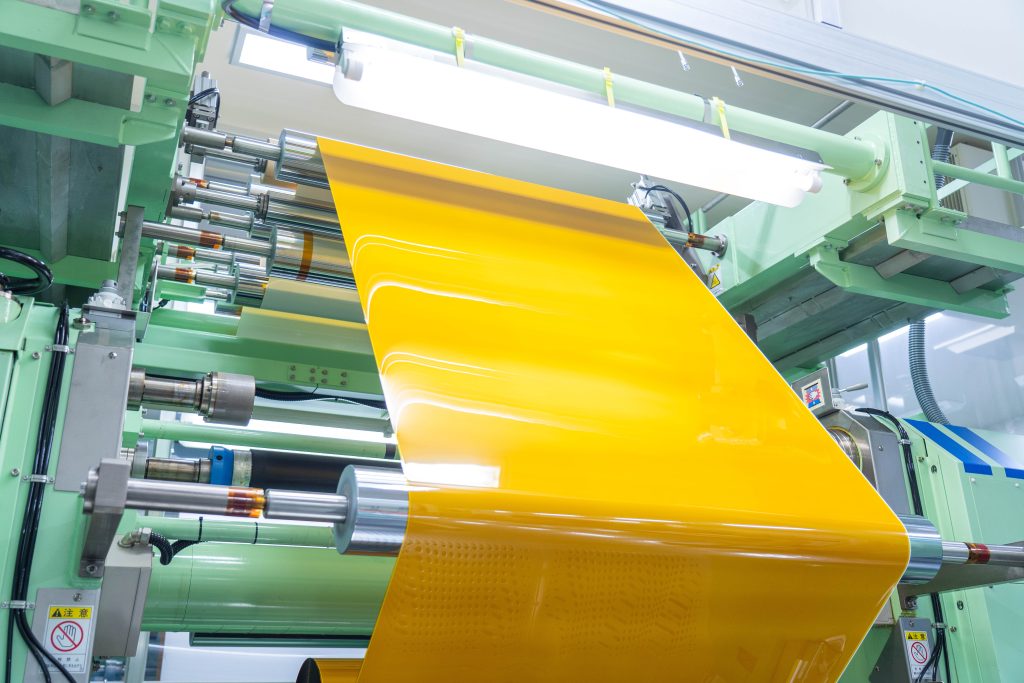
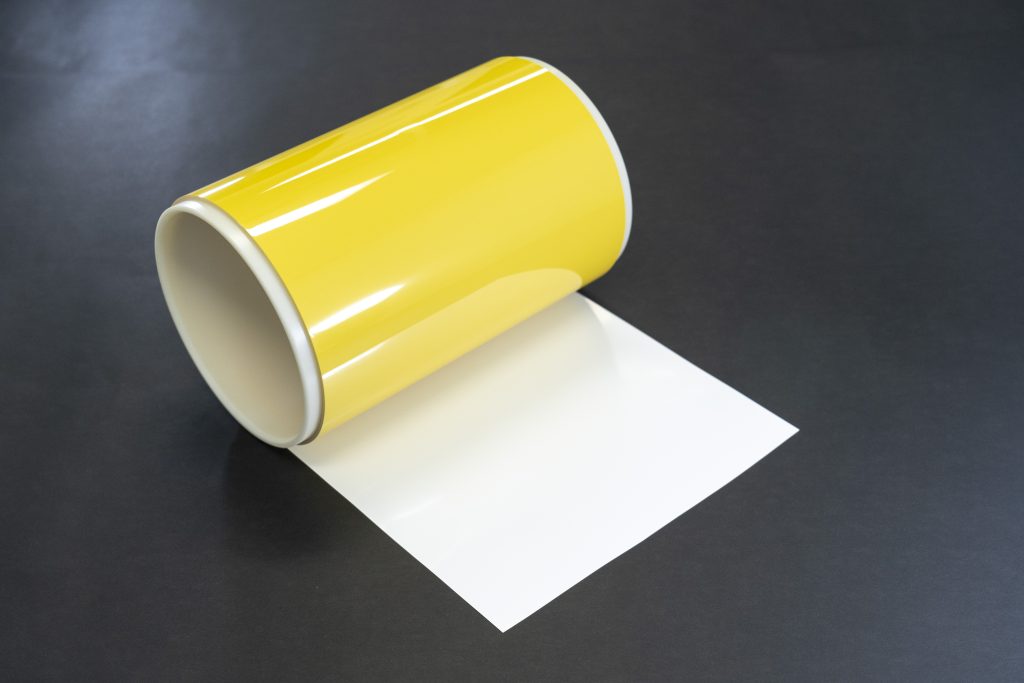
―所属部署と担当されている業務内容を教えてください。
生産本部 生産技術部 電気グループに所属しています。
主に受変電設備の運用や保守、省エネルギーの推進、省エネ法対応を含むエネルギー管理、カーボンニュートラルへの取り組みを行っています。
当社の工場は3拠点ありますが、そのうち隣接している中田原工場と中田原西工場の2拠点を担当しています。
―弊社の商品が必要になった経緯を教えてください。
省エネを推進するためには、装置ごとの電力把握が必要だと感じていました。
しかし、実現するにはクランプメーターや電力計を複数箇所に設置し、データ収集、回収作業…といった工程が必要で、時間がかかることを懸念していました。
また、リアルタイムでデータを確認し、エネルギー使用量の推移を把握できる方法も探していました。
―弊社商品はどちらでお知りになりましたか?
営業担当の方から電話でご紹介いただきました。
工事不要かつクラウドで管理できるということを知り、興味を持ちました。
―以前はどのような方法で電力計測されていたのかを教えてください。
さまざまなメーカーの電力計を導入し、一部ではリアルタイムでデータを把握できるものも設置していますが、基本的には毎月、各受変電設備の電力計を検針し、そのデータをExcelに入力して管理していました。
―その際の課題を教えてください。
1つ目は、設置の際に電源工事や測定箇所の停電工事が必要で、導入コストが高くなるため、測定箇所の増設が難しかったことです。
2つ目は、電力計ごとにデータの取り扱いが異なり、管理方法に差が生じていたことです。データ収集のためのアプリのインストールやサーバー設置には、他部署の協力や専門的知識が必要な場面もあり、増設や導入に手間がかかるため、統一方法を模索していました。
3つ目は、データ収集のために複数の場所を回らなければならなかったことです。ひとつの設備でも、駆動装置やドライヤーなど、いくつかの機器が含まれていて、複数の制御盤が存在します。それらの機器をまとめてモニタリングしようとすると、制御盤の位置が離れているため時間がかかっていました。
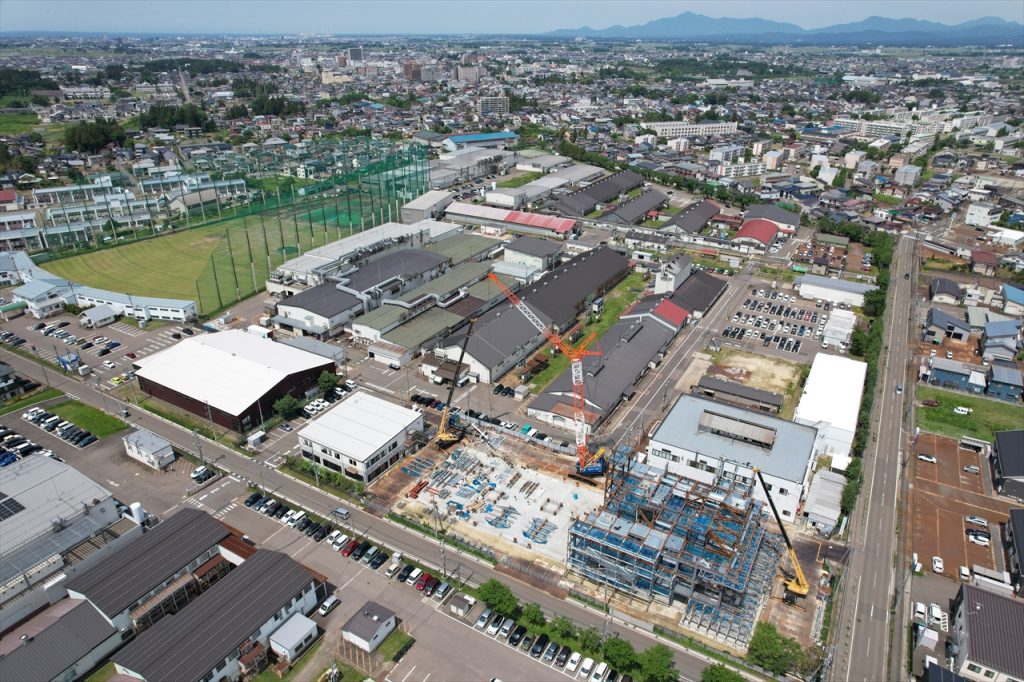
―弊社商品の導入の決め手や、選定において意識されたことを教えてください。
導入の決め手は、停電工事や配線工事が不要だったことです。 クラウドサービスを利用するため、自社サーバーが不要であることもメリットでした。
一方で、電圧が固定値になるため、既存の電力計との誤差が気になりましたが、テスト機を使って他社製品と比較したところ、誤差は許容範囲であり、さらにクラウド上でスケーリングが可能なことから、問題なく運用できることが確認できました。
その際、Bluetoothの通信範囲や安定性についても検証した結果、安定した通信が可能であることも分かり、導入を決めました。
―現在、どのような場所に設置されているか教えてください。
生産設備や、空調機などの設備に対して、10個の電力センサを設置しました。稼働状況の把握や、非稼働時や季節変動による使用量の傾向を把握して、無駄な運転をしていないかの監視を行っています。
はじめは、装置に取り付けてデータを取得した後、取り外して次の装置に付け替える運用を考えていました。しかし、データを見ていくうちに、季節によって変化があることに気付きました。運転状態やパフォーマンスを理解するうえで、こうしたデータは非常に重要ですので、特定の装置に絞って継続的にデータを取りたいという意識が強くなりました。
センサの取り付け作業は基本的に勤務中に行いました。機械が稼働中でも支障なく取り付けることができました。
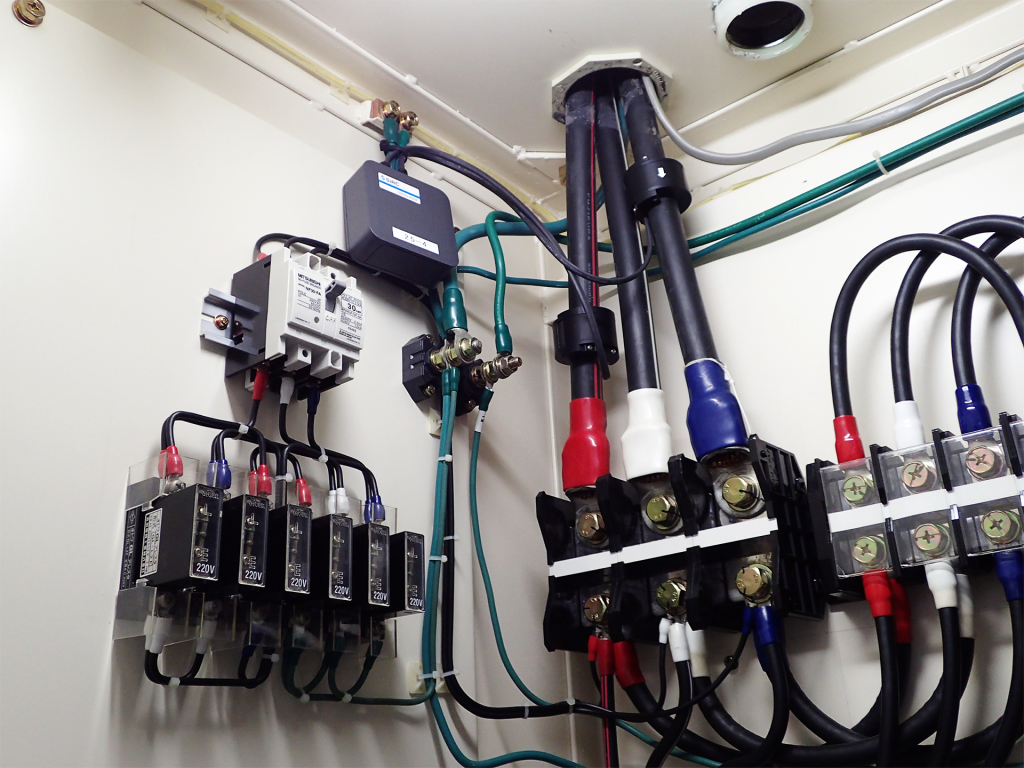
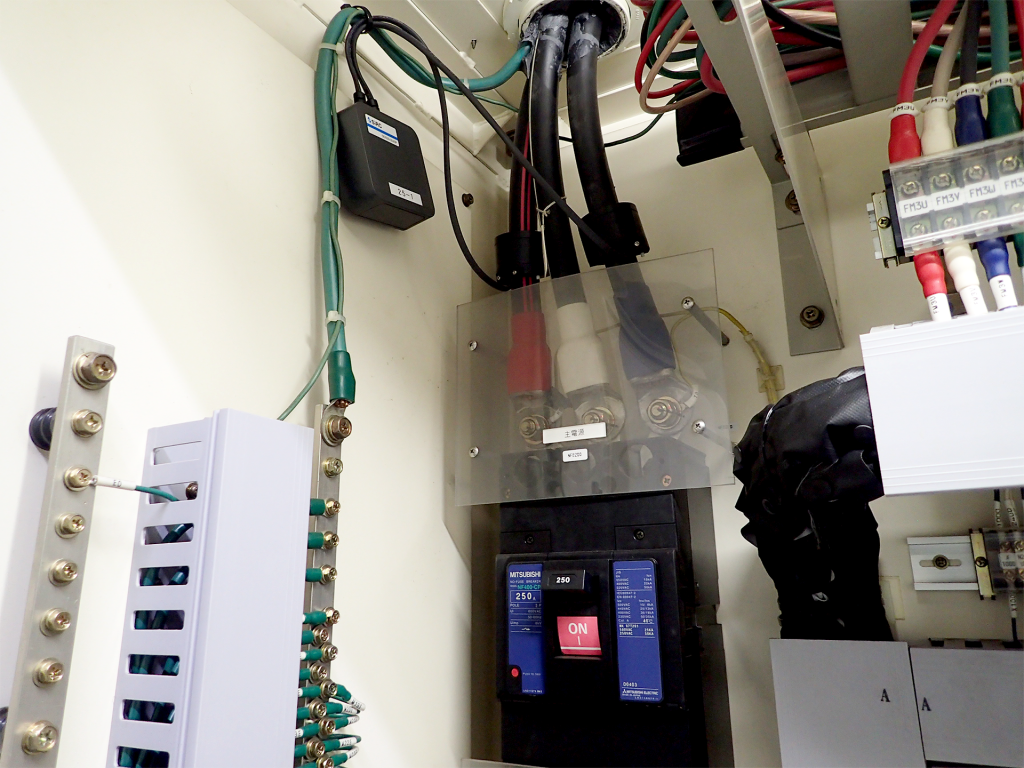
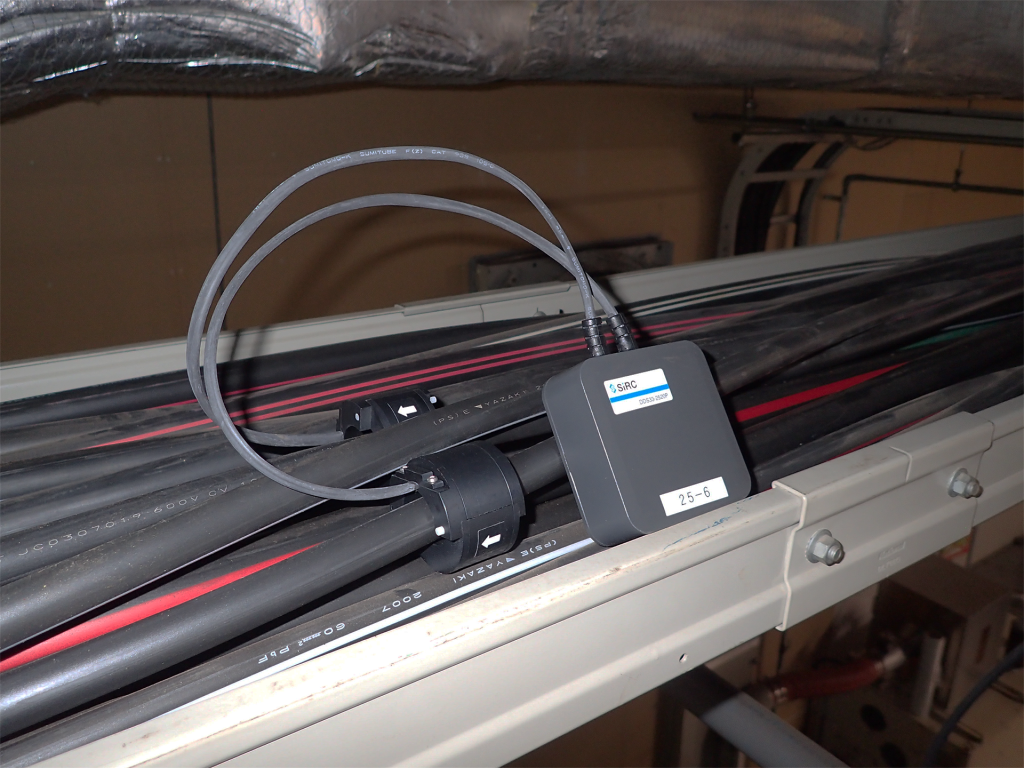
―弊社商品を導入して変わったことや、貢献できていることを教えてください。
設備ごとの電力を見える化することで、エネルギーのムダを把握できるようになりました。
たとえば、設備が稼働していないにもかかわらず空調がフル稼働している場合、稼働状況に応じて空調を最適化するなど、データに基づいた改善提案が可能になりました。
また、手軽に測定箇所を増設できることや、現場の管理者にクラウドサービスの閲覧権限を付与すれば、各自でアクセスし、利用状況を把握出来るようになったのも便利ですね。
―現在の取り組みについて、今後の展望を教えてください。
政府のカーボンニュートラル達成目標は2050年ですが、当社では2030年を目標に前倒しで取り組んでいます。今後は一部の設備群で導入しているこのシステムを他の設備群にも横展開しながら、取り組みを加速させていきたいと考えています。
―導入を悩んでいる企業様へメッセージをお願いします。
設置に伴う配線工事が不要なため、手軽に導入することができました。
電力センサの電池は約3年持ち、電池電圧をクラウド上で常時監視しているため、突然の電池切れの心配もなく運用できています。
導入をスムーズに進めるために、センサと中継器の距離などを、事前に現場で確認しておくと安心ですよ。
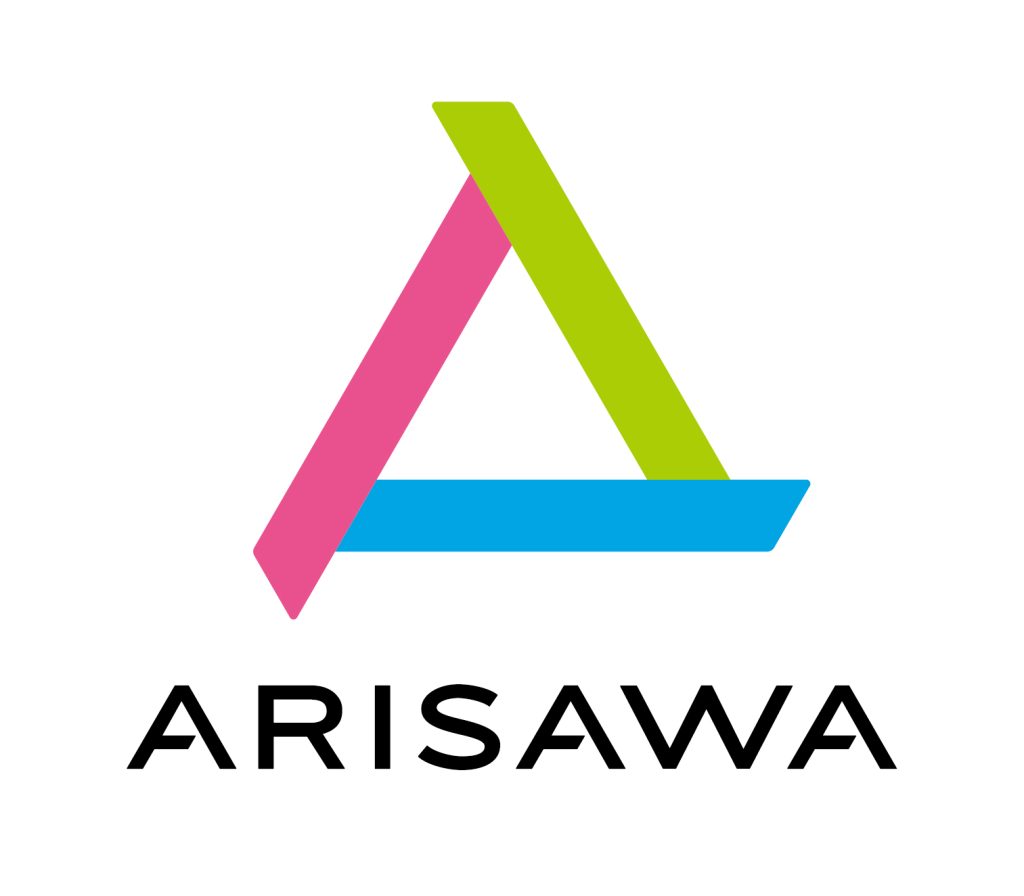

創業 1909年4月8日
代表者 代表取締役社長 有沢悠太
本社所在地 新潟県上越市南本町1-5-5
事業概要 電子材料、産業用構造材料、電気絶縁材料、ディスプレイ材料などの製造・販売
HP https://www.arisawa.co.jp/